Introduction to Carousels
Carousel AS/RS, also known as the industrial carousel, may be integrated with a specific purpose robotic inserter/extractor for small load buffering. This technology finds itself at the heart of systems varying widely in application, from the food industry to the manufacturing floor. It facilitates high speed order picking with limited manual help, thus reducing the need for operators. There are two types of carousels, the vertical carousel system and the horizontal carousel system. We will go in depth regarding the two different types later on.
- + By World Of MHE + -
Automated Storage and Retrieval Systems (AS/RS)
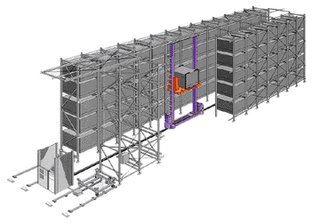 Automated Storage and Retrieval Systems (often referred to as ASRS or AS/RS) refers to a variety of computer-controlled methods for automatically depositing and retrieving loads from defined storage locations. Systems of this nature have been used for years in manufacturing and warehouse facilities. ASRS technology is just beginning to be used in large libraries, particularly at universities. It is used mostly to retrieve seldom-used books and periodicals that are kept in storage vaults. It works via a robotic "arm" that quite literally fetches materials from archival locations. This concept can be applied to a warehouse or distribution centre too! When an order is placed, it will be keyed into the system and the ASRS will automatically retrieve the items on the list, from their various location. This speeds up the order picking process and facilitates the order fulfillment process.
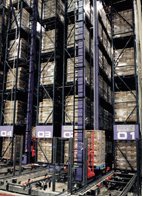
Automated Storage and Retrieval Systems (ASRS) are meant to do high density, hands-free buffering of materials in distribution and manufacturing environments. There are several classes of Automated Storage and Retrieval (AS/RS) that are characterized by weight and size handling characteristics
Unit Load AS/RS machines are generally pallet handling systems with capacities that vary much like lift trucks. Unit load AS/RS Systems are often quite tall and sometimes support the building shell that contains them. The density, security and labor / machinery savings they provide, which makes them a good choice in a variety of applications, from cold storage to general warehousing.
- + By World Of MHE + -
Introduction on Automated Warehouse Systems
Automated Systems Besides the use of manual equipments used to move goods, an automated system may also be used. We will be covering on the 2 main automated systems used by warehouses in the industry. Automation increases the order picking speed and reduces the usage of labor, which is preferred for warehouses to operate efficiently and effectively. They are the Automated Storage and Retrieval System (ASRS), and Carousels.
- + By World Of MHE + -
More about Carousels
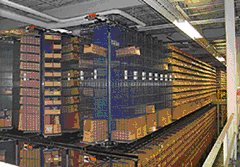
Carousels Turn Inventory Faster Horizontal and vertical carousels are simple, parts-to-picker systems. They keep inventory moving and ready for sudden demand. One picker using two stock-locator driven horizontal carousels can easily pick up to 120 line items per hour. Vertical carousels with pick indicator lights guide the picker to the exact SKU, raising accuracy and throughput even further.
Carousels Handle a Variety of Products Carousels can stage and speed the fulfillment of orders for finished product or bring parts to point of use for assembly, whether the loads handled are large units or hundreds of small components. Each pod presents multiple part numbers to the operator.
Carousels Provide Degrees of Automation When used with appropriate control software, efficient routings can be made that ensure no time is spent waiting for parts to arrive a the pick-point. The newest horizontal carousel systems can be equipped with mechanical extractors to free manpower for other tasks and allow completely automated full-case picking. Replenishment stock can be called up automatically as well, making pick line stock-outs a thing of the past
- + By World Of MHE + -
Horizontal Carousels
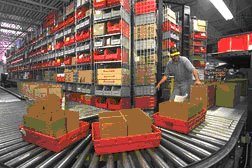
Horizontal Carousels are a system of horizontally rotating shelves that move at your command, delivering items to you and increasing order picking throughput significantly over traditional methods.
- + By World Of MHE + -
Advantages of Carousels
General advantages of carousels Increases productivity up to 600% due to increases picking accuracy, products throughputs, lower inventory levels. Reduces cubic storage space up to 40-60% Shelves travel up to 90 feet per minute 600, 1000, 1500 and 2500 pound capacity 6-12 foot heights available
Regularly scheduled preventive maintenance keeps these productivity tools working for years to come, with no unplanned downtime.
Most carousels are equipped to be moved mechanically so that, even in a power shortage, inventory remains accessible.
Price: ~$40k
- + By World Of MHE + -
Vertical Carousels
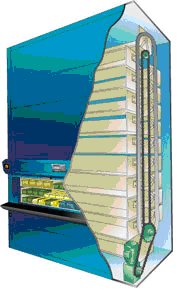
Vertical Carousels consist of rotating shelves that move up or down on response to your commands, delivering items to you at an ergonomically safe and convenient access window. Vertical carousels increase storage density, throughput and efficiency while reducing inventory and required man-hours.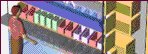
- + By World Of MHE + -
Upcoming trends for MHE - Voice Activated Picking System
The Voice Recognition/Response System allows people with no computer skills to achieve manual sorting/picking by talking with normal conversational speech. This system translates spoken words and numbers into carrier bin numbers or route IDs according to carrier route scheme tables. The carrier codes are displayed or communicated by voice commands to the picker advising them of the bin location. 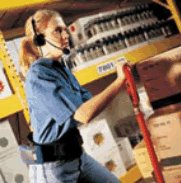 Features and Benefits:
Eliminates necessity for Scheme Memorization Increased Productivity Higher Accuracy No Computer Skills Required Minimizes Time Spent on Employing Training Hands Free
- + By World Of MHE + -
Upcoming trends for MHE - Radio Frequency Identification (RFID)
RFID in the Warehouse can be useful by adding RFID tags to all items and identifying the items.
Example of a RFID tag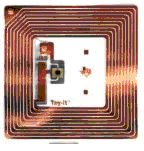
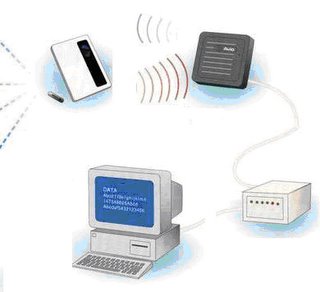
These tagged products are read by receiving and interpreting magnetic waves transmitted by the chip, with the use of an RFID antenna and reader. Information is then transferred to the system. This enables identification of the item without scanning a barcode or manually searching for an item based on its pasted label.
RFID can be read through concrete, so some warehouse operators bury tags in the floor to guide and track RFID-enabled forklifts. The application provides a real-time view of locations, a data point which software application use to improve asset utilization and measure productivity. RFID readers also can be mounted on forklifts or at key storage area entry/exit points to monitor inventory movements. Continual, unattended monitoring can be used to supplement bar code-based inventory control procedures to provide an added degree of visibility to high-value goods. The practice can produce near 100 percent inventory accuracy and eliminate the need for cycle counts and reduce out-of-stock emergencies.
Benefits of RFID for Companies with Warehouse Distribution Operations
RFID solutions from Symbol provide real-time information by automatically detecting product movements throughout the distribution process. RFID technology provides real-time inventory visibility while minimizing the need for manual checks, allowing you to:
Track pallets, cartons and containers with unmatched speed and accuracy Automate product identification and authentication Increase speed and efficiency along with fewer errors throughout the entire distribution process Improve efficiencies for inventory control and reporting Gain greater control over costly material handling assets Improve inventory visibility to feed enterprise systems Reduce stock levels resulting from improved inventory management Automate reporting of all material moves both inbound/outbound and within your facility Increase overall labor productivity
Articles on RFID picking: rfidjournal.com/article/articleprint/496/-1 rfidjournal.com/article/articleprint/366/-1/1/
- + By World Of MHE + -
|